Introduction
In high-precision jewelry manufacturing, every micron matters. A well-executed electroplating process is not just about aesthetics—it determines durability, efficiency, and overall production quality, enhancing brand reputation in the long run.
In the competitive world of jewelry manufacturing, modern electroplating plays a crucial role. It enhances surface quality, improves wear resistance, and ensures long-term value. Professionals in the industry understand that selecting the right electroplating chemicals—whether for pre-treatment, metal deposition, or post-treatment—is essential for meeting market demands. This article explores key solutions that contribute to high-quality surface finishing in jewelry production.
Understanding Electroplating in Jewelry Manufacturing
Reasons for Electroplating Precious Metals
- Enhanced color and appearance: Electroplating with precious metals like gold, silver, or platinum significantly improves the color and finish of the underlying base metal. It provides a richer, more uniform color that helps conceal variations between different parts or solder joints.
- Wide range of colors: This process creates a variety of colors by co-depositing precious metals with other materials, allowing for unique finishes and effects.
- Surface improvement: Electrochemical plating conceals surface defects, such as scratches, tarnish, or irregularities, and enhances the overall appearance. Additionally, it allows base metals or less expensive materials to mimic the look of gold or silver, commonly seen in fashion jewelry.
- Increased durability: The plated layer extends the longevity of a piece, offering additional protection against wear, corrosion, and tarnishing.
Challenges in Electroplating Precious Metals
When plating complex-shaped items or jewelry, several factors must be considered:
- Uniform Coating: Achieving a consistent thickness over intricate designs, sharp edges, and recessed surfaces is essential.
- Strong Adhesion: The plated layer must bond well with the base metal to prevent cracking, peeling, or delamination over time.
- High-Quality Surface Finishing: A smooth, bright, and even finish is key, avoiding defects such as pores, micro-cracks, or rough textures.
- Plating Speed: While high-speed galvanization can improve efficiency, it should not compromise the uniformity or quality of the plated layer.
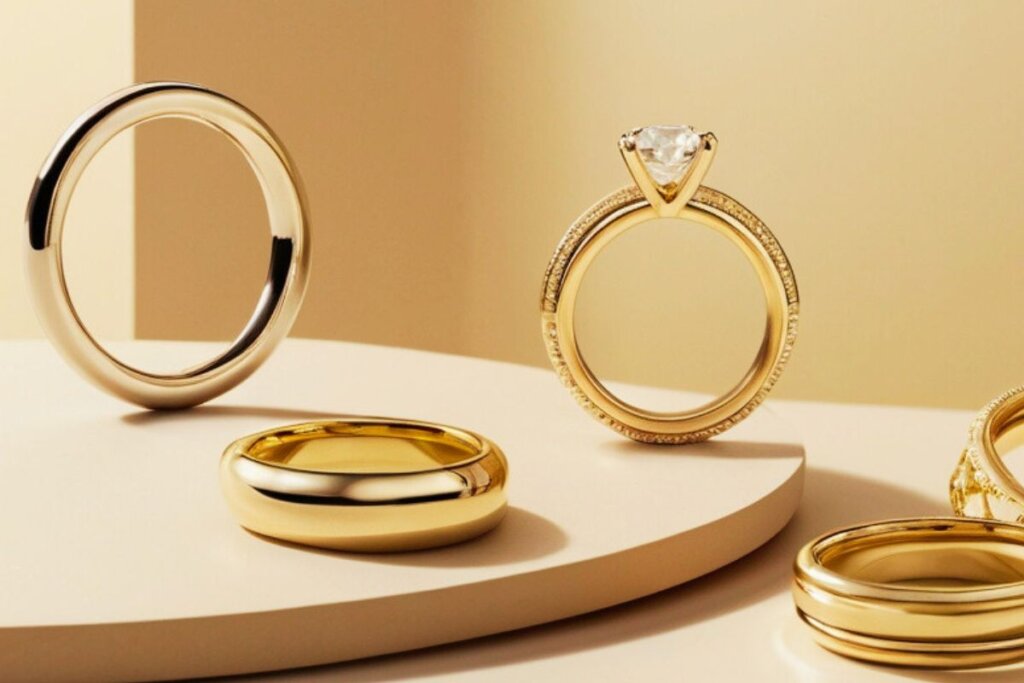
surface quality, improves wear resistance, and ensures long-term value
The Three Major Electroplating Stages and Required Chemicals
1. Pre-Treatment: Preparing the Surface
Before metal deposition, the jewelry surface must be meticulously cleaned and prepared to ensure proper adhesion. This phase includes:
- Degreasing – Removes oils and residues from the metal surface.
- Ultrasonic Cleaning – Uses ultrasonic waves to eliminate fine particles.
- Descaling & Activation – Prepares the metal for optimal adhesion through acidic solutions.
2. Electroplating: Applying Precious Metal Solutions
Metal deposition involves coating a jewelry piece with a thin layer of metal using specialized solutions. Key types include:
- Gold, Silver, and Rhodium Solutions – Provide luxurious finishes and improve durability.
- Platinum and Palladium Solutions – Offer superior corrosion resistance and hypoallergenic properties.
3. Post-Treatment: Enhancing and Protecting the Finish
To ensure longevity and the best appearance, post-plating treatments are essential:
- Nano Coatings – Provide an additional protective layer against tarnish and wear. These Nano Coatings Products can be long-lasting and skin-friendly.
- Decorative Blackening – Adds depth and contrast to designs.
- Sealing & Polishing – Enhances shine and surface smoothness.
Key Factors Affecting Electroplating Quality
To achieve the best results in galvanic plating, several factors must be considered:
- Solution Purity: Contaminated solutions can lead to uneven plating and poor adhesion.
- Electrical Current Control: Incorrect current settings may cause over-plating or weak bonding.
- Bath Temperature: Maintaining an optimal temperature ensures a smooth, uniform finish.
- Plating Time: Over-plating can result in rough textures, while under-plating leads to weak coatings.
Troubleshooting Common Electroplating Issues
Issue: Poor Adhesion of Plating
- Cause: Inadequate surface preparation or contamination.
- Solution: Ensure thorough degreasing, activation, and rinsing before plating.
Issue: Uneven Plating or Dark Spots
- Cause: Inconsistent electrical current or impure plating solution.
- Solution: Regularly filter and replenish solutions, and verify power settings.
Issue: Tarnishing or Discoloration Over Time
- Cause: Exposure to environmental factors or lack of post-treatment protection.
- Solution: Apply nano coatings or protective sealants to extend longevity.
Conclusion
Galvanization is a crucial step in jewelry manufacturing, ensuring high-quality finishes and long-lasting durability. By understanding the right chemicals and techniques for pre-treatment, plating, and post-treatment, jewelry manufacturers can enhance their production efficiency and product quality. Investing in modern electroplating solutions will help businesses remain competitive in the ever-evolving jewelry industry.
For expert insights and premium surface finishing solutions, get in touch with us today by filling out the contact form below—our team is here to help you achieve the best results!