Einführung
In der hochpräzisen Schmuckherstellung zählt jedes Mikrometer. Ein gut durchgeführter Galvanisierungsprozess dient nicht nur der Ästhetik – er bestimmt die Haltbarkeit, Effizienz und Gesamtqualität der Produktion und trägt langfristig zum Ruf einer Marke bei.
In der wettbewerbsintensiven Schmuckbranche spielt die moderne Galvanotechnik eine entscheidende Rolle. Sie verbessert die Oberflächenqualität, erhöht die Widerstandsfähigkeit gegen Abnutzung und sorgt für einen langfristigen Werterhalt. Fachleute in der Branche wissen, dass die Wahl der richtigen Elektrolyte – sei es für die Vorbehandlung, die Metallabscheidung oder die Nachbehandlung – entscheidend ist, um den Marktanforderungen gerecht zu werden. Dieser Artikel stellt die wichtigsten Lösungen für eine hochwertige Oberflächenveredelung in der Schmuckproduktion vor.
Die Bedeutung der Galvanisierung in der Schmuckherstellung
Gründe für die Galvanisierung von Edelmetallen
- Verbesserte Farbe und Optik: Durch die Galvanisierung mit Edelmetallen wie Gold, Silber oder Platin wird die Farbe und Oberfläche des Grundmetalls erheblich verbessert. Sie sorgt für eine gleichmäßige, intensive Farbgebung und verdeckt Unterschiede zwischen verschiedenen Teilen oder Lötstellen.
- Große Farbvielfalt: Durch das Co-Abscheiden von Edelmetallen mit anderen Materialien entstehen verschiedene Farben, die einzigartige Effekte und Oberflächen ermöglichen.
- Oberflächenveredelung: Die galvanische Beschichtung kaschiert Oberflächendefekte wie Kratzer, Anlauffarben oder Unregelmäßigkeiten und verbessert das Gesamtbild. Zudem können unedle Metalle oder günstigere Materialien durch Galvanisierung das Aussehen von Gold oder Silber annehmen, was häufig bei Modeschmuck zu sehen ist.
- Erhöhte Haltbarkeit: Die galvanische Schicht verlängert die Lebensdauer eines Schmuckstücks und bietet zusätzlichen Schutz gegen Abnutzung, Korrosion und Anlaufen.
Herausforderungen bei der Galvanisierung von Edelmetallen
Bei der Beschichtung von Schmuck mit komplexen Formen müssen mehrere Faktoren berücksichtigt werden:
- Gleichmäßige Beschichtung: Eine gleichmäßige Schichtdicke über komplizierte Designs, scharfe Kanten und vertiefte Oberflächen ist entscheidend.
- Starke Haftung: Die Metallbeschichtung muss sich fest mit dem Grundmaterial verbinden, um Risse, Ablösungen oder Delamination im Laufe der Zeit zu vermeiden.
- Hochwertige Oberflächenveredelung: Eine glatte, glänzende und gleichmäßige Oberfläche ist essenziell, um Defekte wie Poren, Mikrorisse oder raue Texturen zu vermeiden.
- Beschichtungsgeschwindigkeit: Eine hohe Galvanisierungsgeschwindigkeit steigert die Effizienz, darf aber nicht auf Kosten der Gleichmäßigkeit oder Qualität der Beschichtung gehen.
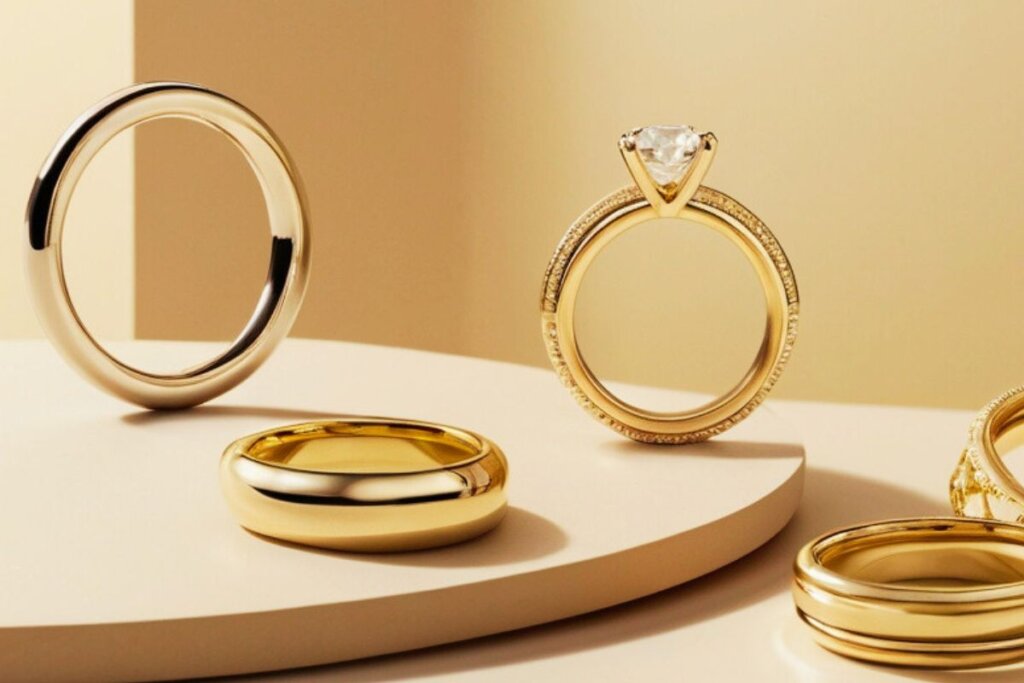
Oberflächenqualität, verbessert die Verschleißfestigkeit und sichert den langfristigen Wert
Die drei Hauptphasen der Galvanisierung und die benötigten Elektrolyte
1. Vorbehandlung: Vorbereitung der Oberfläche
Vor der Metallabscheidung muss die Schmuckoberfläche gründlich gereinigt und vorbereitet werden, um eine optimale Haftung zu gewährleisten. Dieser Schritt umfasst:
- Entfetten – Entfernt Öle und Rückstände von der Metalloberfläche.
- Ultraschallreinigung – Nutzt Ultraschallwellen, um feinste Partikel zu lösen.
- Entzundern & Aktivieren – Bereitet das Metall durch saure Lösungen auf eine optimale Haftung vor.
2. Galvanisierung: Aufbringen der Edelmetalllösungen
Bei der Metallabscheidung wird das Schmuckstück mit einer dünnen Metallschicht überzogen. Wichtige Elektrolyte sind:
- Gold-, Silber- und Rhodiumlösungen – Sorgen für eine luxuriöse Oberfläche und verbessern die Haltbarkeit.
- Platin- und Palladiumlösungen – Bieten eine hohe Korrosionsbeständigkeit und hypoallergene Eigenschaften.
3. Nachbehandlung: Schutz und Veredelung der Oberfläche
Zur Sicherstellung der Langlebigkeit und der besten Optik sind Nachbehandlungen unerlässlich:
- Nano-Beschichtungen – Schützen zusätzlich gegen Anlaufen und Abnutzung. Diese Nanobeschichtungsprodukte können langanhaltenden und hautverträglichen sein.
- Dekorative Schwärzung – Verleiht Designs mehr Tiefe und Kontrast.
- Versiegelung & Polieren – Sorgt für zusätzlichen Glanz und eine glatte Oberfläche.
Wichtige Faktoren für eine hochwertige Galvanisierung
Um optimale Ergebnisse bei der galvanischen Beschichtung zu erzielen, sind mehrere Faktoren zu beachten:
- Reinheit der Elektrolytlösung: Verunreinigte Lösungen können zu ungleichmäßiger Beschichtung und schlechter Haftung führen.
- Kontrolle des elektrischen Stroms: Falsche Einstellungen können zu einer Überbeschichtung oder schwachen Haftung führen.
- Badtemperatur: Eine optimale Temperatur ist entscheidend für eine gleichmäßige und glatte Oberfläche.
- Beschichtungszeit: Eine zu lange Galvanisierung kann raue Texturen verursachen, während eine zu kurze Zeit zu dünnen und instabilen Schichten führt.
Häufige Probleme und Lösungen bei der Galvanisierung
Problem: Schlechte Haftung der Beschichtung
- Ursache: Unzureichende Oberflächenvorbereitung oder Verunreinigung.
- Lösung: Gründliches Entfetten, Aktivieren und Spülen vor der Galvanisierung sicherstellen.
Problem: Ungleichmäßige Beschichtung oder dunkle Flecken
- Ursache: Inkonsistente elektrische Stromstärke oder verunreinigte Elektrolytlösung.
- Lösung: Regelmäßige Filtration und Nachfüllung der Lösungen sowie Überprüfung der Stromversorgung.
Problem: Anlaufen oder Verfärbungen im Laufe der Zeit
- Ursache: Einfluss von Umwelteinflüssen oder fehlender Schutz nach der Beschichtung.
- Lösung: Nano-Beschichtungen oder Schutzversiegelungen anwenden, um die Haltbarkeit zu verlängern.
Fazit
Die Galvanisierung ist ein entscheidender Schritt in der Schmuckherstellung, um hochwertige Oberflächen und langlebige Veredelungen zu gewährleisten. Durch das Verständnis der richtigen Elektrolyte und Techniken für die Vorbehandlung, Galvanisierung und Nachbehandlung können Schmuckhersteller ihre Produktionseffizienz und Produktqualität steigern.
Die Investition in moderne Galvanisierungslösungen hilft Unternehmen, in der sich ständig weiterentwickelnden Schmuckbranche wettbewerbsfähig zu bleiben.
Für professionelle Beratung und hochwertige Lösungen zur Oberflächenveredelung – kontaktieren Sie uns über das untenstehende Formular. Unser Expertenteam unterstützt Sie gerne bei der Optimierung Ihrer Produktion!